AAL is an Open 60-style yacht made of volcanic fibres. It is designed to be sustainable, and to sail a complete around the world loop that includes the Arctic and Antarctic Oceans
Les Sables d’Olonne is used to waving off circumnavigators – the Vendée Globe, and most recently the Golden Globe, solo skippers start and return from the French Atlantic town.
But on Sunday, 21 July, a particularly extraordinary singlehanded circumnavigation began from Les Sables. Austrian skipper Norbert Sedlacek is bidding to sail a five ocean 34,000-mile ‘double loop’ around the world in AAL, an experimental yacht built from volcanic fibres.
AAL – which stands for AntArcticLab – may look like a conventional carbon racing IMOCA at first glance, but this robust design has been modified to contend with North West Passage ice floes, as well as complete a full Southern Ocean loop.
Sedlacek did not set out to build an Open 60, much less launch a new boatyard, or take on a five-ocean record attempt, or become an expert in experimental chemical engineering – but over the past decade has found himself doing all of those things.
After competing in the 2008/09 Vendée Globe, Sedlacek began investigating the potential of volcanic fibres as a more sustainable material for yacht construction. His work attracted investment from a wealthy Austrian industrial family, which funded early testing of the material.
“We met at some coming together of Austrian high society,” Sedlacek recalls, “and we said we’d build a new Open 60 – so now we’re really doing this!” There were, he admits, some cocktails involved. The initial materials tests were promising, but he says: “In reality it was far away from manufacturing on an industrial level.”
Article continues below…
Ràn VII: On board the Stealth Bomber of the Fast 40+ class
Some boats are the sum of their parts, but Rán VII is really the sum of the parts that aren’t…
Veedol: On board Yoann Richomme’s record-breaking Lift 40
A curious pattern repeated in the 2018 Route du Rhum, as the newest designs – like the foiling Ultimes, and…
To test the concept, Sedlacek and his team first built an ‘Open16’ FipoFix. Essentially a 1:3.75 scale version of the 60, it was made in 2013 using the volcanic fibre material. “We shrunk it. The 16-footer had all the items of the 60-footer: canting keel; ballast tank.
“My son started sailing it on the Spanish coast, and then sailed non-stop to Palm Beach and non-stop on the northern transatlantic route back to Les Sables. That was really cool and, for us, was proof of the concept.”
Basalt boats
However, working with an unproven material meant that no existing boat yard wanted to take on the risks and challenge of getting the 60-footer certified. Having discussed all the options with his backers, Sedlacek took a new direction: they would retain the patents and machinery, and instead start a new shipyard. Innovation Yachts was formed in late 2014.
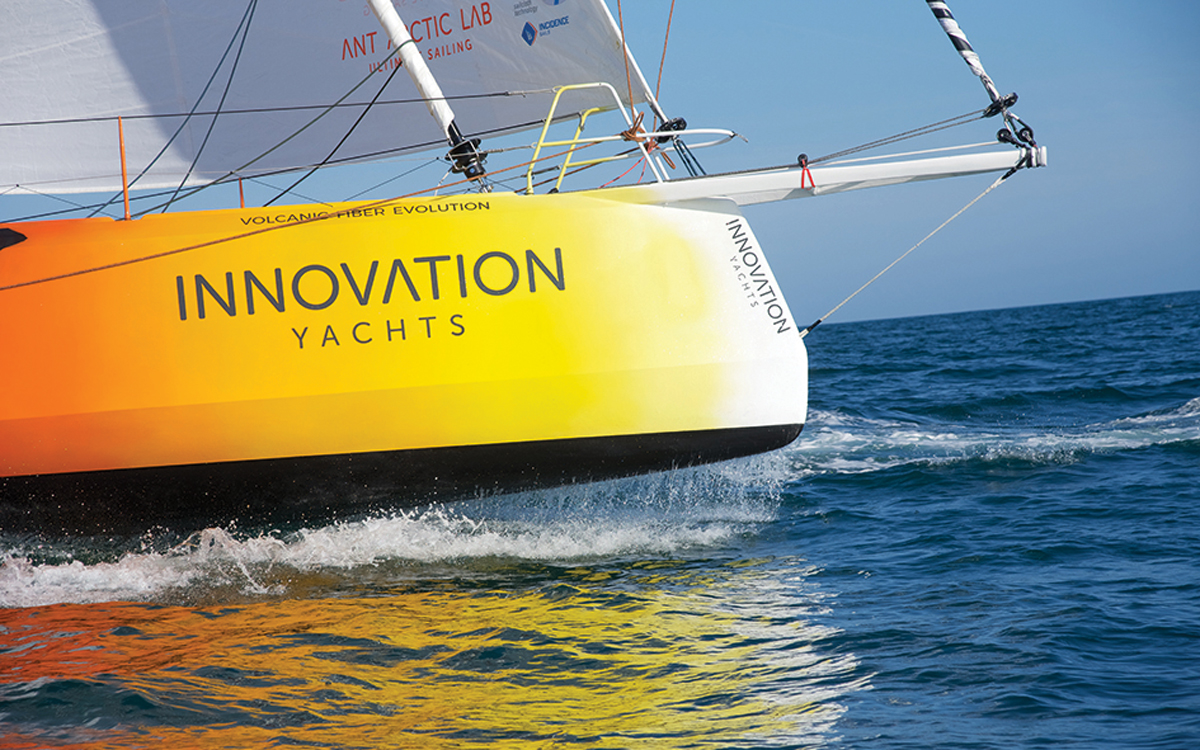
The entire bow area is reinforced monolithic construction for nudging ice out of the way. Photo: Pedro Rodriguez
The inspiration for an ice-going yacht was an event called the Star Arctic Race, which was planned to sail from New York to Vancouver via the North West Passage in 40-footers made using volcanic fibres. But when the event folded Sedlacek decided to build his own 60-footer and to instead sail a new around the world course, taking in the Arctic and Antarctic Oceans.
The volcanic fibre properties are, according to Sedlacek, ideal for creating a yacht to sail through light ice, being both shock absorbing and with a very hard surface. It is hydrophobic, extremely resistant to high temperatures and UV damage, and impact resistant.
Unlike carbon, which shatters when it fails, Sedlacek says the volcanic fibre laminates break layer by layer, making it less likely to give rise to a sudden catastrophic failure.
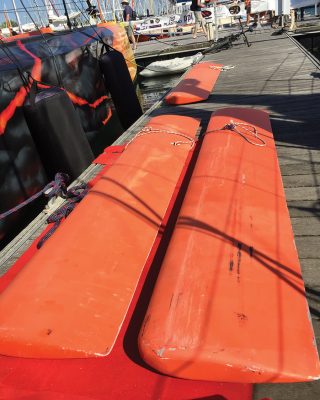
There are three boards, two interchangeable daggerboards and one central canard to protect the keel fin. Photo: Pedro Rodriguez
In terms of costs, Sedlacek estimates that building from volcanic fibres cost around a third of an equivalent carbon build, with performance characteristics that are comparable or better to a high quality glassfibre build.
The real advantage, however, lies in the material’s ecological credentials. The volcanic basalt itself is naturally occurring, plentiful and much more easily recycled than either glassfibre or carbon fibre.
“We shred all the material left over, and we make new panels out of that, or flower pots, or a toilet. Minus the dust, we use 100% of the leftovers
to bind with new matrix systems and make new materials,” he explains.
“And it means it is absolutely not more expensive to pay a little bit more for the fibre, because we give the promise that if you bring the boat back we will buy the material back. Because for us it’s a building material, it has a value.”
The other construction materials used in the yacht have also been carefully chosen – FCC-certificated balsa wood from Ecuador, and low-emission medical grade epoxy.
The major design differences between AAL and a conventional IMOCA 60 relate to the ice stages and sheer length of the voyage – Sedlacek estimates the circumnavigation will take in the region of nine months.
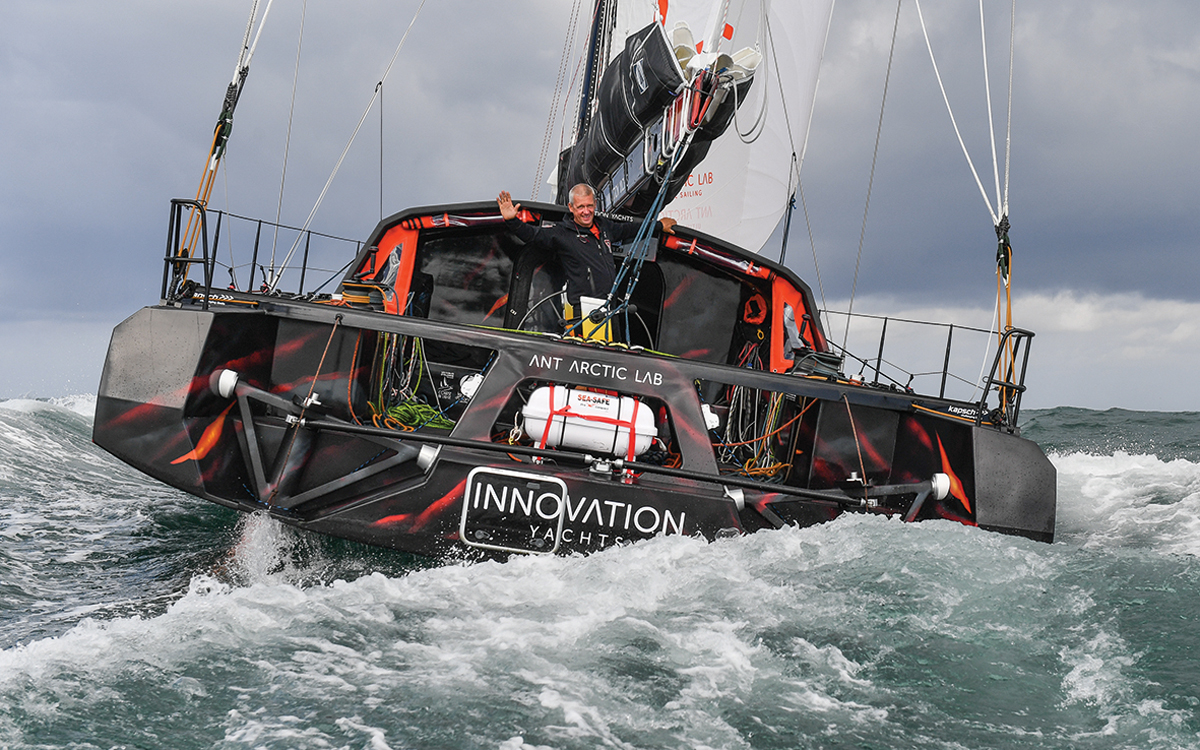
There are 73 watertight compartments across the hull
“The boat has a lot of parameters to meet, to be able to sail fast in low wind conditions, like we will have in the north, and on the other hand the boat must be strong and powerful enough to survive in the deep south.”
Growler-proof
The entire bow area is heavily reinforced against growlers and the lower hull is double-skinned, while the corners are also reinforced. All the frames and stringers are significantly chunkier than on a racing IMOCA, and within the structure multiple watertight compartments have been created to guard against sinking in the event of a hull breach.
Besides two conventional daggerboards, AAL has a third canard just in front of the canting keel. “We designed the central one to protect the keel fin when you go through ice.”
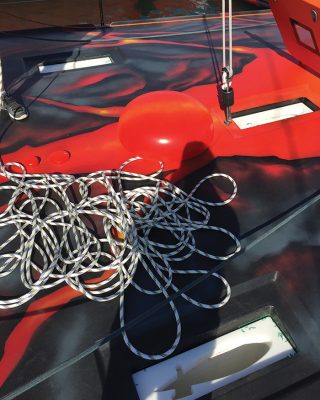
The three daggerboard positions, with reinforced housings, and satellite communications dome. Photo: Pedro Rodriguez
He plans to reduce speeds to 3-5 knots when in the ice regions. “When you reach Greenland you put the central board down, and then when you’re out of the Baring Sea you bring it up and hope that nothing’s floating.”
The port and starboard boards are thicker and lower aspect than racing designs, and interchangeable in case one is damaged by ice or other debris. All are made from volcanic fibre.
The keel itself is very close to the design of the current IMOCAs, although the fin chord is a little thicker. The hull area around the keel meanwhile is also heavily reinforced.
Sedlacek says they based their calculations on a full grounding at a maximum hull speed of around 13 knots, which requires the structure to withstand an equivalent load of 172 tonnes – achieved through over 400 layers of fibre.
Fossil free circumnavigation
As he wants to complete his voyage without fossil fuel, AAL has two Oceanvolt electric sail drive engines to be used as hydrogenerators, as well as solar panels.
Sedlacek estimates that the substantial battery banks will give him around 8-10 days worth of autonomous power while going through the ice region – although he will be sail-powered the entire way.
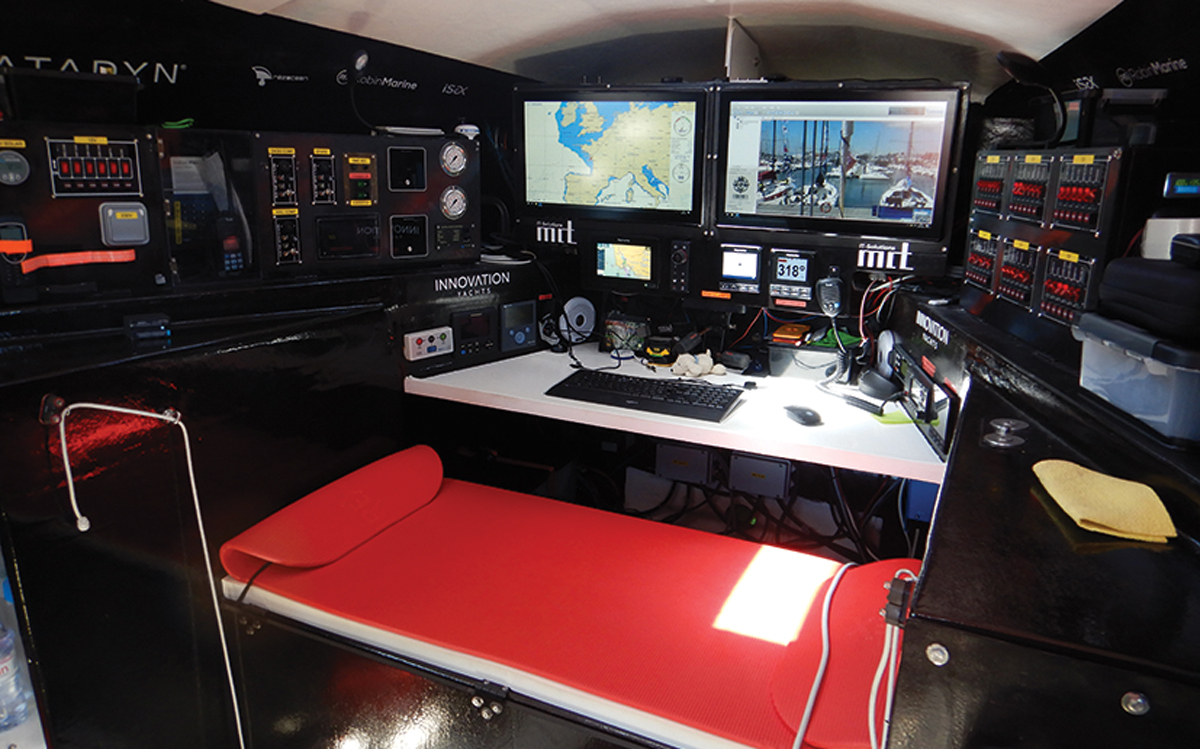
AAL has duplicate nav stations with redundancy built into all the systems. Photo: Pedro Rodriguez
It is an exceedingly ambitious aim. Twice Sedlacek has set off only to turn back shortly after to deal with technical issues (after this July’s start he was forced back to Les Sables d’Olonne again after suffering sail and rig damage), and the North West Passage is notoriously capricious. His next attempt is likely to be in 2020.
Specification
LOA: 18.28m (60ft 0in)
Beam: 5.82m (19ft 1in)
Draught: 4.50m (14ft 9in)
Displacement: 9,500kg (20,944lb)
Mainsail: 170m² (1,830ft2)
Gennaker: 400m² (4,306ft2)
Storm jib: 20m² (215ft2)
Energy: 2xOceanvolt SD10 (10KW), 8 fixed solar panels (400W), 2 portable solar panels (100W)